Touch sensors that don’t even need direct contact offer new sensitivity for robotic 3D structure recognition and wireless transmission of data
Published : Apr 02,2024 / DOI : 10.1080/14686996.2024.2311635
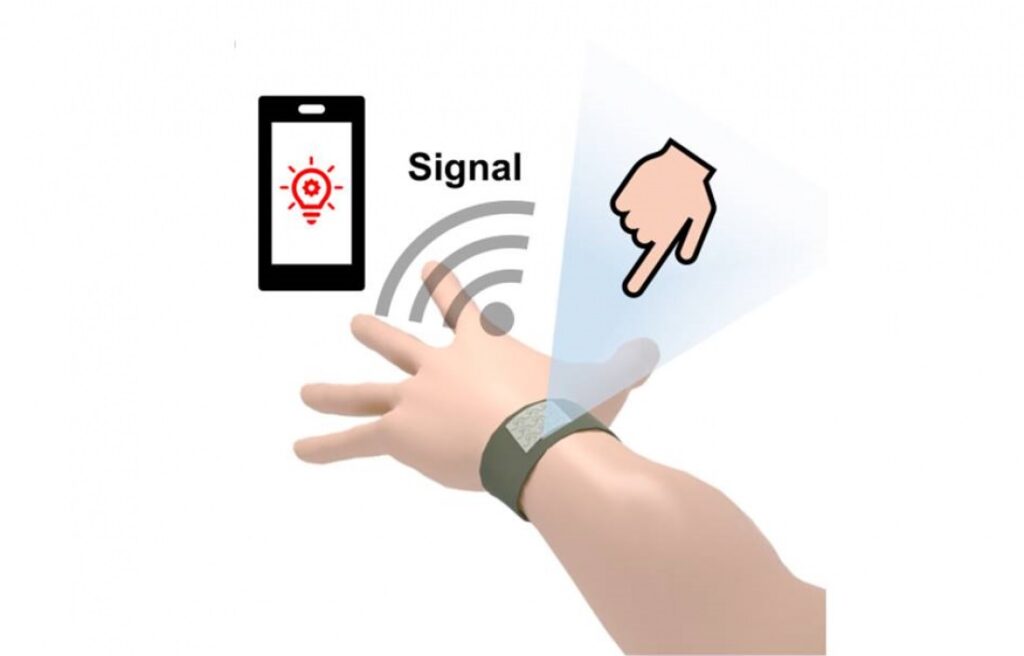
A radical new type of touch sensor for robotics and other bio-mimicking (bionic) applications is so sensitive it works even without direct contact between the sensor and the objects being detected. It senses interference in the electric field between an object and the sensor, at up to 100 millimetres from the object. The researchers at Qingdao University in China, with collaborators elsewhere in China and South Korea, describe their innovation in the journal Science and Technology of Advanced Materials.
Electronic skins have become a crucial element in bionic robots, allowing them to detect and react to external stimuli promptly. This can allow robotic systems to analyse an object’s shape, and, if required, also to pick it up and manipulate it.
The sensors in most current systems rely on direct touch causing a physical deformation of a contact layer, leading to changes in electrical capacitance. Unfortunately, the uniformity of the response to different regions limits the sensitivity and overall abilities of such systems.
“To bring greater sensitivity and versatility we have developed new composite films with surprising and very useful electrical properties,” says Xinlin Li of the Qingdao University team.
The most surprising aspect came when the researchers combined two materials with a high dielectric constant – a measure of their response to electric fields. This composite had an unexpectedly low dielectric constant, a counter-intuitive result which is ideally suited to making a sensor that is more sensitive to electric fields.
The composite consists of small amounts of graphitic carbon nitride added to polydimethylsiloxane. It can be made and processed by a specific 3D printing method, called dispensing printing, that offers fine control over the structure and pattern of the printed high-viscous ink. The team used this to make a grid that could sense objects while between 5 and 100 millimeters away from the object’s surface. They tested the grid’s capabilities by using the researchers’ fingers as the objects being detected, as they approached close to the grid but without actually making contact.
“The performance was outstanding, in terms of sensitivity, speed of response and robust stability through many cycles of use,” says Li. “This opens new possibilities in the field of wearable objects and electronic skin.” She adds that it is suitable for making the physically flexible sensors needed for wearable technologies. These could be applied for medical monitoring, or more general uses in the fast developing ‘internet of things’(IoT), involving remote control of a wide variety of appliances.
Incorporating the sensing grid into a printed circuit board allowed the data it collects to be transmitted over the 4G networks widely used by mobile phones.
The team now plan to refine the technology with a view to develop its suitability for mass production. They also want to explore further possibilities beyond merely detecting shape and movement. For example, different units in the sensor array have the ability to respond sequentially, which provides the possibility of realizing human-computer interaction, such as gesture recognition. The performance of the sensors in the contact and non-contact system also reflects its potential in human motion detection, such as obstacle avoidance and gait monitoring, which could be applied in intelligent medical care.
Further information:
Xinlin Li
Email: xinlin0618@163.com
Qingdao University
Paper: https://doi.org/10.1080/14686996.2024.2311635
About Science and Technology of Advanced Materials (STAM)
Open access journal STAM publishes outstanding research articles across all aspects of materials science, including functional and structural materials, theoretical analyses, and properties of materials. https://www.tandfonline.com/STAM
Dr Yasufumi Nakamichi
STAM Publishing Director
Email: NAKAMICHI.Yasufumi@nims.go.jp
Information
- Authors
- Bingxiang Li, Xianbin Zheng, SeHyun Kim, Xuhao Wang, Fuhao Jiang, Rong Li, Sang Woo Joo, Chenhao Cong & Xinlin Li
- Citation
- Sci. Technol. Adv. Mater. Vol. 25 (2024) 2311635
- URL
- https://doi.org/10.1080/14686996.2024.2311635