Half a century of metal testing aims to make Japan’s industries safe.
Published : January , 2020 / DOI : 10.1080/14686996.2019.1680574
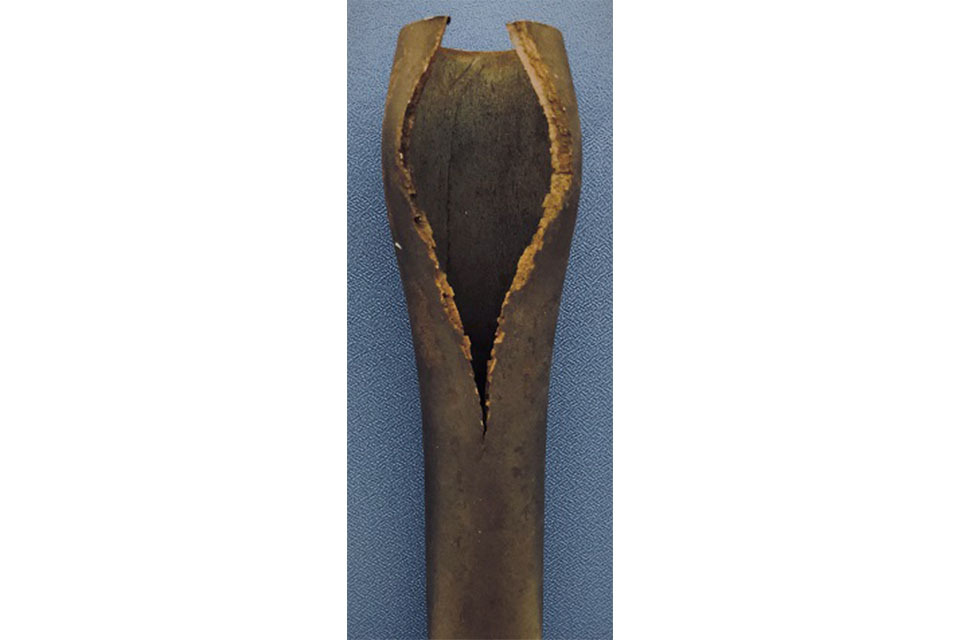
For the past 50 years, researchers at the National Institute for Materials Science (NIMS) have been conducting detailed short- and long-term testing of a wide variety of structural materials manufactured in Japan to ensure they can withstand long-term stresses. Now, NIMS scientists have reviewed this data, in the journal Science and Technology of Advanced Materials, summarizing the institute’s major findings.
In 1966, NIMS’s predecessor, the National Research Institute for Metals, launched its ‘creep data sheet project’. The aim of this project was to determine the stress required to rupture heat-resistant steels and alloys in 100,000 hours (about 11.4 years) at high temperatures. This ‘creep rupture strength’ data was initially needed to determine the allowable stresses metals could be exposed to in power plants. But more recently, this data has been used to assess how much longer power plant parts have before they begin to wear and tear.
Just over a decade later, in 1978, NIMS also began assembling what has become a huge database of fatigue properties of structural materials used in numerous industries, including automobiles and aircrafts. Fatigue describes how cracks propagate in a metal over time. Fatigue tests involve placing a metal sample under repetitive loads, called cycles, to see how long it takes for a crack to develop and propagate. These tests are conducted at room temperature and high temperatures. Samples are exposed to a relatively small number of cycles (in the range of 10 million cycles) or up to 10 billion cycles, lasting for several years.
NIMS data has revealed that the long-term creep strength of materials varies, and that scientists need to choose the type of analysis method for creep rupture data according to the type of material. How creep happens in materials during testing not only depends on the amount of stress applied, but also on the temperature conditions. The researchers have found that materials react differently to varying temperature depending on their chemical composition, the amounts of minor elements in them, and the crystal grain size. Ferritic heat-resistant steels, which are commonly used in thermal power plants, were found to have very long-term, inherent creep strength. But this creep strength is dependent on the amount of minor solutes present in the steel.
Fatigue limits, on the other hand, are affected by a metal’s tensile strength and hardness. Interestingly, NIMS scientists have found that some metals can last for an incredibly long time without forming cracks as long as they are constantly exposed to room temperatures. These same metals, however, would eventually form cracks if exposed to the same stress but at high temperature.
Up until now, the creep and fatigue data sheets developed at NIMS have been used mainly for industrial purposes. The institution is now aiming to improve accessibility so the data can also be used by academics.
Further information
Kota Sawada
National Institute for Materials Science
SAWADA.Kota@nims.go.jp
Yoshiyuki Furuya
National Institute for Materials Science
FURUYA.Yoshiyuki@nims.go.jp
Papers
https://doi.org/10.1080/14686996.2019.1697616
https://doi.org/10.1080/14686996.2019.1680574
About Science and Technology of Advanced Materials Journal
Open access journal STAM publishes outstanding research articles across all aspects of materials science, including functional and structural materials, theoretical analyses, and properties of materials.
Shunichi Hishita
STAM Publishing Director
HISHITA.Shunichi@nims.go.jp
Information
- Authors
- Yoshiyuki Furuya, Hideaki Nishikawa, Hisashi Hirukawa, Nobuo Nagashima & Etsuo Takeuchi
- Citation
- Sci. Technol. Adv. Mater.20(2019)1055.Sci. Technol. Adv. Mater.20(2019)1055.
- URL
- http://doi.org/10.1080/14686996.2019.1680574
- Authors
- Kota Sawada, Kazuhiro Kimura, Fujio Abe, Yasushi Taniuchi, Kaoru Sekido, Takehiro Nojima, Toshio Ohba, Hideaki Kushima, Hideko Miyazaki, Hiromichi Hongo & Takashi Watanabe
- Citation
- Sci. Technol. Adv. Mater. 20 (2019)1131.
- URL
- https://doi.org/10.1080/14686996.2019.1697616